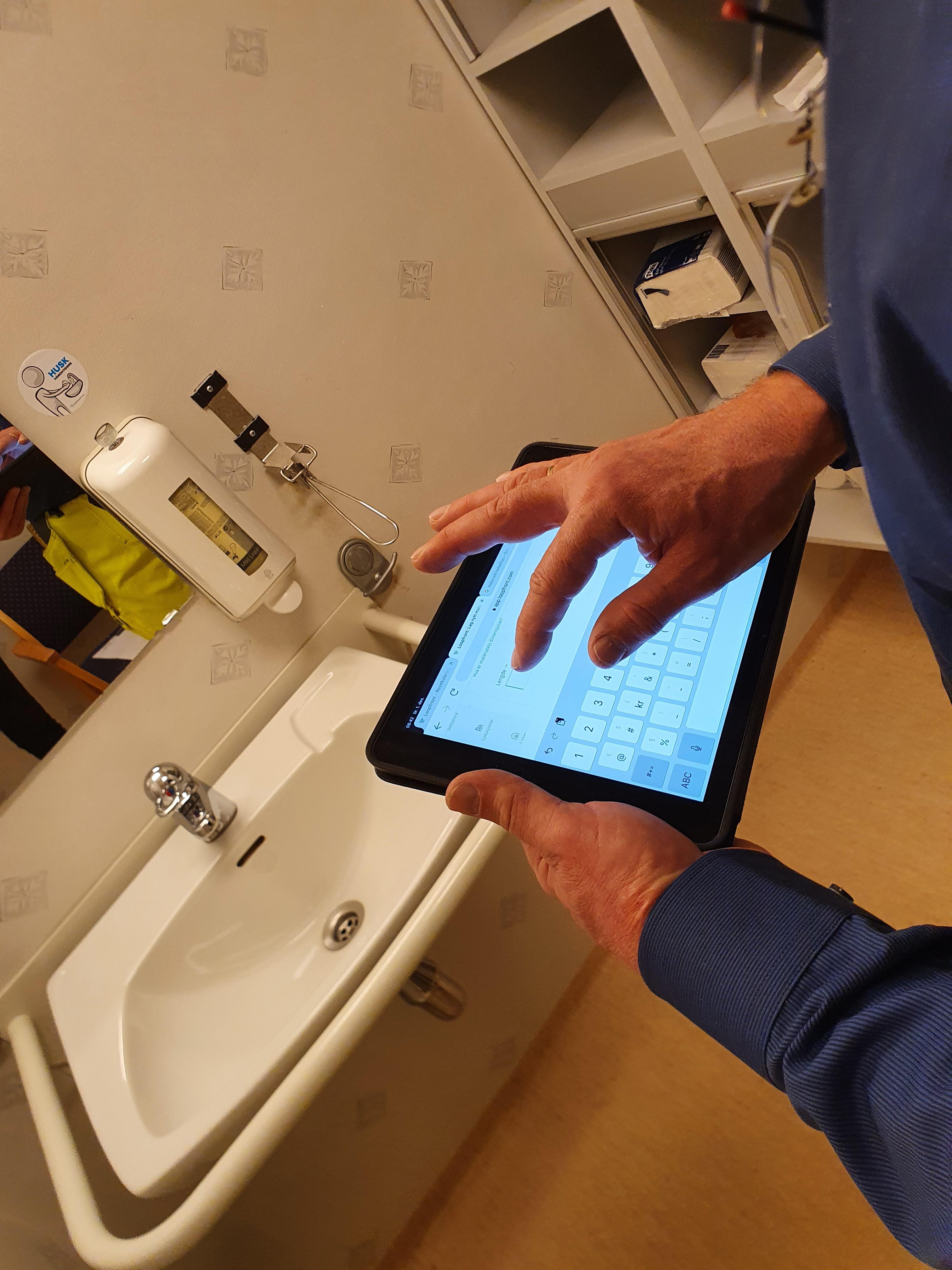
During this year, several municipalities and organizations in Scandinavia have mapped over 30,000 materials in Loopfront for reuse, repair and redesign. This is a trend that has come to stay! With increasing interest and initiatives for reuse of building materials worldwide, both public and private stakeholders are working to create a new norm with reuse.
Two regional reuse networks with a dozen real estate companies are now being established in Oslo and Trondheim. The networks will make it easier to reuse building materials in the rehabilitation or demolition of buildings.
Multiconsult, Norwegian engineering consultancy
Many people are still unsure of which building materials can be reused and not, considering what is justifiable according to regulations. Safety is extremely important when it comes to the rehabilitation and replacement of specific parts of buildings. The same applies if, for example, you are buying a used car. We are familiar with Mandatory roadworthiness tests for used cars: Then it is professionals who confirm whether the car is in accordance with EU regulations for vehicles.
In the same way, we have building codes and regulations in the construction industry, therefore it is important to engage consultants with high competence in materials and reuse. These professionals can comment on further use in accordance with the regulations. As with a car, its not a guarantee, but professional assessment we can trust when we get in a used car and drive 80 km per hour.
Eirik Rudi Wærner is an Environmental Consultant at Multiconsult and makes professional assessments of building materials and building components for reuse. We have joined him on re-use surveys in Trondheim and in the Oslo region. The materials have been mapped in Loopfront's cloud-based database, using tablets. Eirik explains how to make assessments during the material surveying:
What's important to think about when doing surveys like these?
First, we must consider "what is reusable, can it be dismantled, what is practically possible to remove from a building". And then we have to register in relative detail. If an architect is going to use this material for designing, they need to know the exact dimensions. For instance, we have measured glass partitions, office partitions and doors. And it turns out that there are many different widths and heights. All this is important because it is difficult to cut and adjust it once it is manufactured.
How does one proceed to evaluate a material, and what should be focused on?
Here it is possible to have several thoughts in your head at the same time. One can focus entirely on finances and building code requirements, but one can also consider greenhouse gas savings and reduction of the environmental footprint in general. This will depend on the circumstances of the project and the client's focus.
Example: In Longyearbyen (Svalbard) transport economy has a greater focus than elsewhere. Waste must be transported 1000 km to the mainland and all new building materials are transported just as far back. If the client is particularly concerned about the climate, making CO2 savings visible can be more important than saving money.
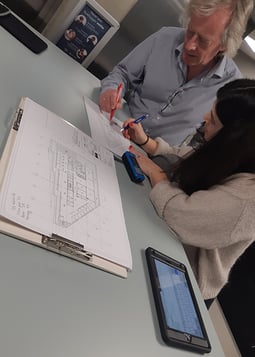
How can one assess if, for example, a door meets building code requirements?
In general, there is no requirement for sound attenuation in all doors. You can use an undocumented door where there is no requirement for sound attenuation, and you can reuse a 25 dB door. there is a requirement for 35 dB attenuation.Then you may have to buy new doors where, for example,
Most fire doors have serial numbers, which makes it possible to find documentation. The next question is if the door shows any sign of wear or damage that will make it unsuitable. Then you actually have to go into the details of the harmonized standard (or building code) to see what is written there.
Why should materials be surveyed early in the project ?
The earlier we map materials, the longer it will be available for other projects. And the greater the probability is that we will find someone who can reuse, for example, these partitions we have registered.
We are dependent on someone having either exactly the same floor height, or who can adapt their building to this floor height / these partitions. On the other hand, if these options doesn't work, they cannot use it directly. There are so many different variables to take into consideration. Ceiling height, colors and so on. So the earlier we start, the greater the probability of finding an heir.
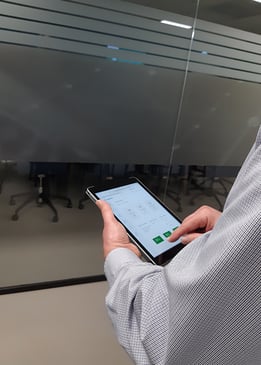
Why do you choose to use Loopfront instead of, for example, Excel?
Multiconsult has a collaboration agreement with Loopfront. We see that as a database solution, this is definitely what we need. Public organizations, such as municipalities, can register everything for internal sales of materials.
Private companies can also have an internal market for their buildings. Or they can choose to make the materials available to others. Then users can go into the database and browse materials. There are different target groups, and Loopfront is a good solution, as they give full overview of materials in the relevant market.
Related Posts
Better Buildings with Reuse
SINTEF writes in their report, Reuse of building materials - Market, drivers and barriers, about ...
Building a market for used building materials
The potential for reuse of materials used in the construction industry is huge. Recently, the ...
Circular economy platform Loopfront raises $6m USD
Loopfront – the digital circular management platform for business and government – announces an ...